Keep up with your boiler’s demanding appetite for coal!
When you’re supplying power to hundreds of thousands of homes and businesses, the demand for your product never takes a break. Neither does your boiler’s demand for coal. So your conveyor equipment better be able to keep feeding it without fail. And because a coal-fired power plant can consume thousands of tons of coal every day – as well as the limestone used to control emissions – your conveyor systems have to be able to take a constant beating.
With coal, if you don’t have a system in place to contain the material during transport, it gets everywhere. Clouds of coal dust get suspended in the air. Some coal spills off the conveyor belt, especially at the transfer points, and it sticks easily to the walls of chutes, pipes, bins and silos, causing material flow issues. These problems can lead to serious safety and health risks for workers and can damage your equipment over time. Plus, when coal dust becomes suspended in the air, it can eventually accumulate on the floor and on your equipment. Or it can be inhaled by workers and cause health problems or even ignite and cause a deadly explosion.
At Martin Engineering, we have over 70 years of experience working with coal, from the mine to the boiler and practically everything in between. All around the world, you can find coal-fired power plants that have installed our products to make their conveyor belts run better by keeping the belts clean, preventing misalignment and keeping fugitive dust under control.
The bottom line is this: the conveyor systems that move coal from the railcar or barge through the crushers and silos all the way to the boiler are complex pieces of equipment, with lots of moving parts that have to work together with precision. When the belt is even a little out of alignment, especially at the transfer points, fugitive material spills and coal dust starts filling the area. Martin products are engineered to keep your conveyor systems cleaner, safer and more productive.
The Best Guarantee in the Business = Zero Risk for You!
Since 1944, Martin has been serving the needs of coal-fired power plants, and literally "wrote the book" on global best practices when it comes to moving bulk materials in it's Foundations™ series of training and textbooks. Today, we have thousands of customers, many of them power plants, who rely on our products to work hard and keep working for a long time. We want you to feel that same high level of confidence in the equipment you use, which is why we back our equipment with a 100% Money-Back Guarantee.
So, if you’re experiencing too many conveyor equipment failures, too much fugitive dust, or the equipment just doesn’t seem to be working the way it should, give us a call. With over 70 years in this business, the problem is most likely something we’ve already dealt with… and solved! Our engineers and technicians are the best in the business and dedicated to helping you improve your business, so contact a Martin representative today.
- Move material more efficiently along conveyor systems and minimize carryback
- Keep downtime for maintenance and housekeeping to a minimum
- Reduce spillage and equipment damage by keeping conveyor belts aligned
- Manage airborne dust and minimize the risk of explosion and inhalation
- Eliminate the need for workers to enter confined spaces
- Prevent material from spilling off of moving conveyors
- Deliver more product by maximizing your mine’s overall throughput
- Reduce costs by minimizing waste and reducing energy consumption
- Eliminate excessive downtime for maintenance and cleanup
CleanScrape® Cleaner Improves Operations At Coal-Fired Power Plant
Coal-Fired Power Plant Needed Solution To Conveyor Belt Mistracking
Air Cannons Knock Down Sticky Coal From Hopper Walls
Coal-Fired Power Plant Applauds MartinPLUS® Services Installation Team
Coal Conveying System Plagued By Dust, Spillage and Carryback
Belt Cleaner And Washbox™ Reduce Carryback By 99%
Air Cannons Dramatically Improve Employee Safety
Belt Cleaners Save Client $100K Per Year
Air Cannons Put An End To Manual Clean Out
Chute Clogging And Spillage Corrected With CleanScrape® Cleaner
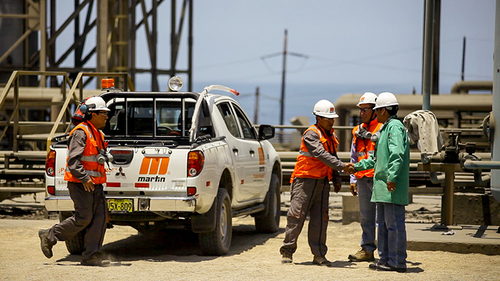
Free Engineering and Application Assistance
Our technicians have solved problems for people in your industry all over the world. Take advantage of our wealth of knowledge. Tell us about your situation today to learn how Martin can improve your performance, safety and bottom line - with no obligation. We want to ensure that you choose the right solution for your exact needs and we are willing to invest the time upfront to get it right the first time.
Briefly Describe Your Application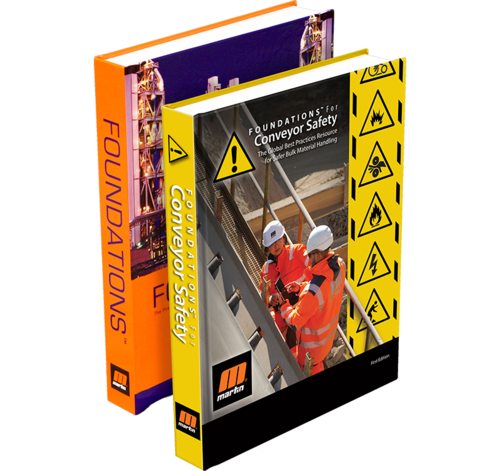
Foundations™ for Conveyor Safety
Learn to Calculate your Return on Conveyor Safety™ with our compilation of worldwide best practices for safer bulk material handling in this first-ever textbook dedicated exclusively to the safety of conveyor systems.
Request Your FREE PDF or Hard-Back Copy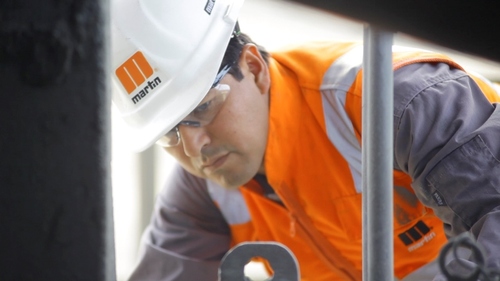
Save With Our MartinPLUS® Walk the Belt™ Service!
Every conveyor is different, even within the same facility! We can provide regularly-scheduled reviews of your bulk material handling system components, involving a specialized crew with the expertise necessary to achieve high operating standards, keeping the conveyor system running at maximum productivity. Immediate data and photos will be available to facility managers and our suggestions will ensure long-term savings and efficiency.
Get Your Belts Reviewed By People Who Know What They’re Looking At -- At No Charge!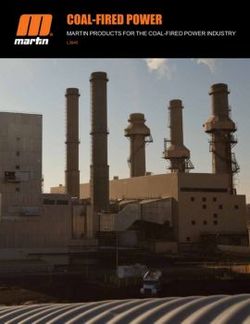
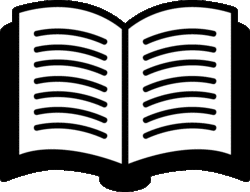
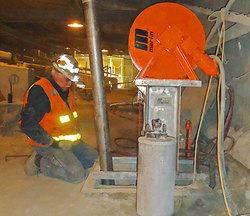