Optimize your operation’s efficiency.
In an industrial environment where tons of material are being unloaded from containers, transported along conveyor belt systems and funneled through chutes, efficiency is critical. With so many moving parts in the process, they have to be precisely coordinated to make sure that the product is moved efficiently without spilling or sticking to the conveyor belt.
When problems occur, materials accumulate quickly. It can build up on the belts and result in carryback or it can adhere to the interior walls of chutes and containers, especially if the material retains moisture. In addition to the loss of product, this also creates obstructions that can hinder or damage the equipment. In extreme situations, particularly at the tail section of conveyor belts, components can be completely buried by spilled material. This frequently causes a shutdown that requires manual cleanup. This is not only inefficient… it can be hazardous for the workers.
If your operation would benefit from an increase in efficiency, talk to one of our experts and ask about our Walk The Belt™ program, where we perform a thorough inspection and assessment of your entire conveyor system. We’re standing ready to listen to you describe your operation and offer recommendations on how to optimize your efficiency. Our technicians and engineers are available to provide expert advice and assistance on all of your bulk material handling questions and problems.
MartinPLUS® Offers Process Improvement Recommendations in Coal-Fired Power Industry
Sugar Processor Hires Martin Engineering For Systems Analysis
Martin® Self Adjusting Skirting Maintains Effective Seal Without Maintenance
Plant Needed Solution To Coal Dust Fire Hazard
Transfer Point Products Improve Severe Spillage And Dust Problems
Martin® Air Cannons Result In No More Unscheduled Outages
Martin Creates Long-Term Solution To Material Flow Problems
Air Cannons Eliminate Need For Water Blasting
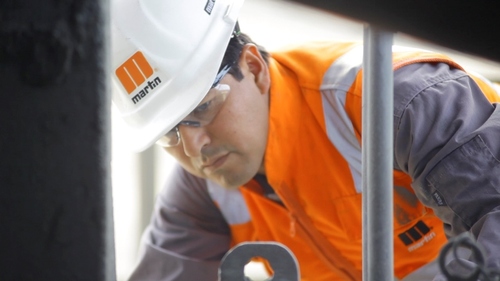
Save With Our MartinPLUS® Walk the Belt™ Service!
Every conveyor is different, even within the same facility! We can provide regularly-scheduled reviews of your bulk material handling system components, involving a specialized crew with the expertise necessary to achieve high operating standards, keeping the conveyor system running at maximum productivity. Immediate data and photos will be available to facility managers and our suggestions will ensure long-term savings and efficiency.
Get Your Belts Reviewed By People Who Know What They’re Looking At -- At No Charge!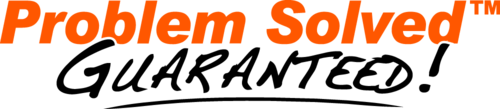
We've solved your problem somewhere before!
While your problem seems unique and frustrating, with 70+ years of solving similar problems around the world, and with the most experienced and educated people on our teams, we can assure you that we’ve “Been There, Done That.” At least close enough to know what needs to be done next and adjust for your situation.
Put Us To The Test For Free! Let Us Give You a Solution.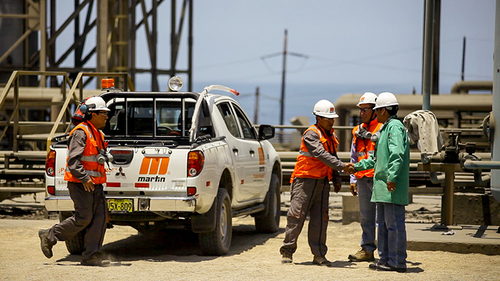
Free Engineering and Application Assistance
Our technicians have solved problems for people in your industry all over the world. Take advantage of our wealth of knowledge. Tell us about your situation today to learn how Martin can improve your performance, safety and bottom line - with no obligation. We want to ensure that you choose the right solution for your exact needs and we are willing to invest the time upfront to get it right the first time.
Briefly Describe Your Application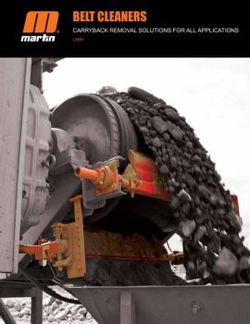
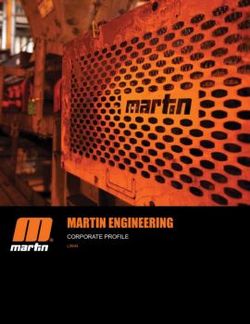
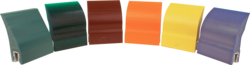