Products Used | ApronSeal™ Single Skirting HD , Dust Curtain |
---|---|
Product Types Used | Belt Cleaning Solutions , Dust Management and Containment Solutions , Transfer Point Solutions , Belt Sealing , Dust Containment |
Industry | Coal-Fired Power |
Customer | Hibbing Public Utilities in Hibbing, Minnesota |
Problem
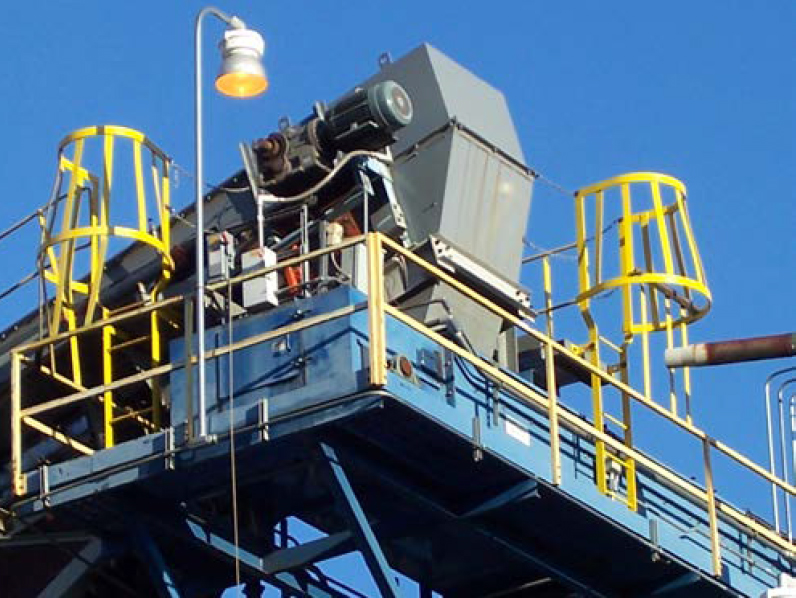
The Minnesota power generating facility was having trouble controlling dust and spillage and preventing fugitive material from reaching nearby homes and businesses. Part of the problem occurred on the three air-supported conveyors which containted some sections with very steep angles. With variable size and moisture content of the fuel, chips would fall back down. Reducing material turbulence during transfer is essential to prevent fugitive dust.
Solution
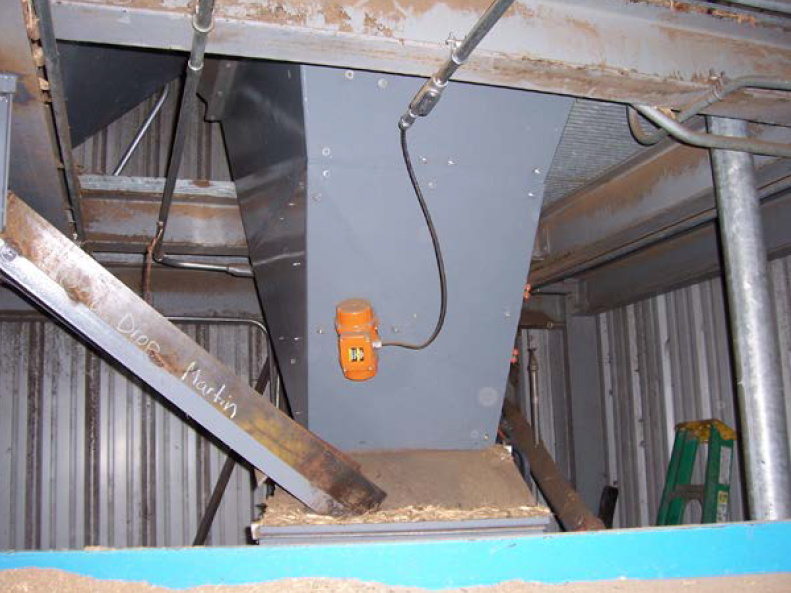
“We installed electric brush cleaners on each conveyor, because they’re very effective on the type of cleated belts used at this facility,” observed Martin Engineering Territory Manager Tom Hines. “The rotating brush delivers good cleaning performance in difficult applications, including belts with ribs, grooves or chevrons, and belts carrying sticky materials or stringy fibers.” Martin Engineering technicians removed troublesome sections of the air-supported conveyor and replaced them with specially engineered transfer points.
They also modified existing transfer points, installing drop chutes to help eliminate dust and transfer chutes with a hood-and-spoon design to improve the material flow. The installation team also placed electric rotary vibrators in key locations inside drop chutes to reduce the potential for plugging. To further ensure control of fugitive material, settling zones were created at the transfer points to slow the air speed, with dust curtains to contain airborne particles. Skirtboard sealing systems were installed on the sides of the loading zones to contain dust, eliminate spillage and reduce cleanup.
Results
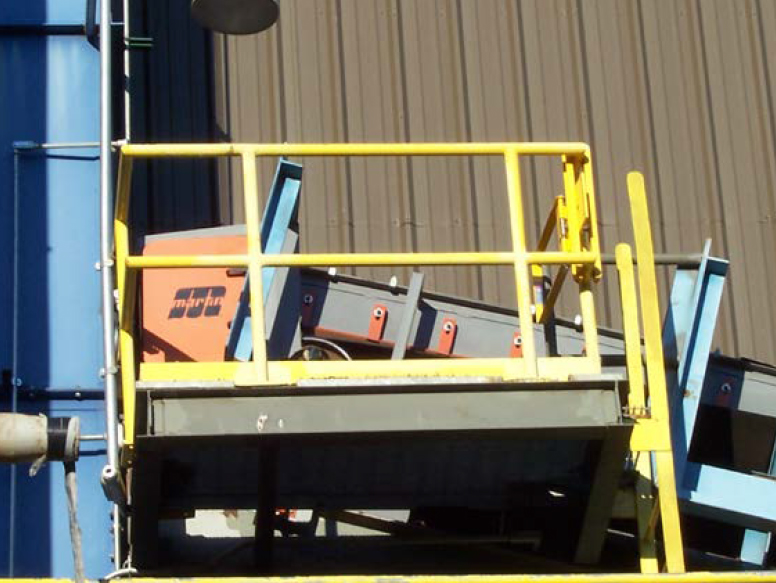
With the modifications in place, HPU reports significant reductions in spillage and airborne dust. “We’re very pleased with the results we’ve seen in fugitive material control,” Gary Myers, Assistant General Manager and Director of Power Production reported. “We’re now reviewing several other conveyor sections to determine the opportunities for additional dust control measures. Our goal has always been to provide the Hibbing area with safe, reliable power that’s produced and delivered in an environmentally-responsible manner, and this work is a reflection of that commitment.” Company officials have been so satisfied with the upgrades from Martin Engineering that they are considering additional A new head chute and brush cleaner were system enhancements to several other conveyors.
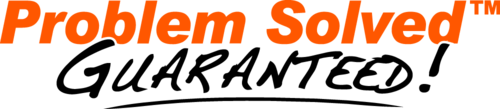
We've solved your problem somewhere before!
While your problem seems unique and frustrating, with 70+ years of solving similar problems around the world, and with the most experienced and educated people on our teams, we can assure you that we’ve “Been There, Done That.” At least close enough to know what needs to be done next and adjust for your situation.
Put Us To The Test For Free! Let Us Give You a Solution.